Warehouse management in other words Warehouse Management Systems (WMS) have been around since the earliest computer systems and provide simple storage functions. Today, a WMS system can be standalone or part of an Enterprise Resource Planning (ERP) system and can include complex technology such as Radio Frequency Identification (RFID) and voice recognition. However, the basic principle of the warehouse system remains the same, which is to provide information that will allow efficient management of the movement of materials in the warehouse.
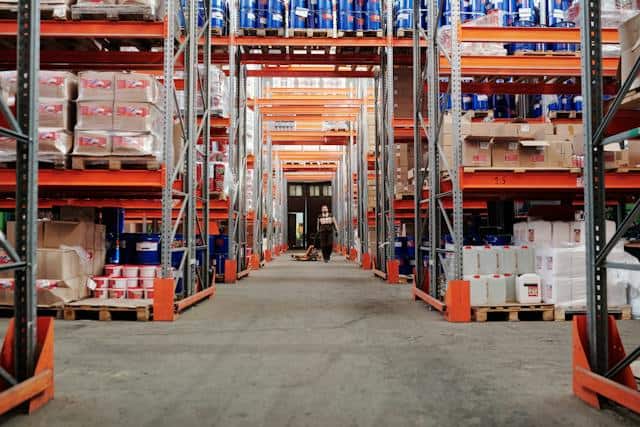
What is a warehouse management system?
A warehouse management system is a set of programs that automates warehouse operations. Warehouse management is the effective and successful execution of a company’s storage and shipping operations. Note that these procedures should be performed professionally with the help of a specialist. Properly executing storage and supply processes will enable brands to run their warehouse operations more safely and efficiently. Today, many e-commerce brands focus on warehouse management processes to dominate their processes.
Proper management of warehouse, which is a part of warehouse operations, will prevent problems that may arise in procurement processes. Because details such as transaction costs and customer satisfaction in the purchasing process are very important for brand prestige. At the same time, the problem of storing missing or excess products will also arise with unhealthy warehouse management. This means an additional financial burden for the brand. It is a system that allows you to manage all processes, from the receipt of the product to the shipment of the company.
The warehouse management system includes the following processes:
Production
receipt of goods
Warehouse management
Census
Shipping
Handling of pallets
These processes ensure the successful implementation of warehouse management systems. Thanks to this, the problems that will be experienced in warehouse management processes will be eliminated and a much more effective management process will emerge. In particular, the above-mentioned processes play an important role in product placement and protection.
Cargo transported by air transport and railway transport is first placed in warehouses and then loaded on transport vehicles.
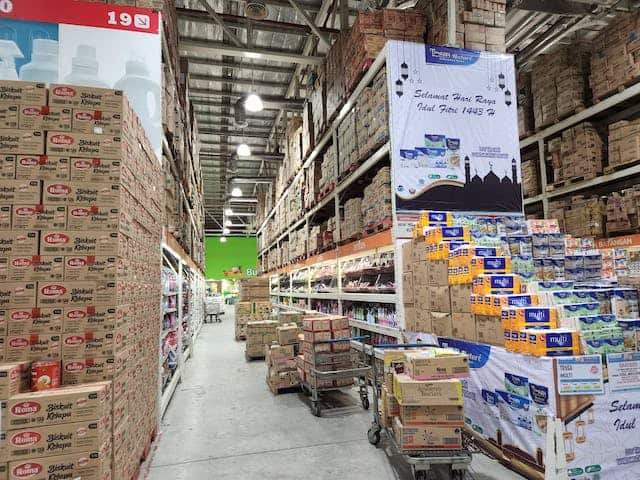
Effective Warehouse Design: Best Ways to Store Product
With the increasing diversity of logistics operations, suppliers and business models, warehouses play an increasingly integral role in supply chains. Therefore, now more than ever, warehouses must provide flexibility, availability and efficient functionality.
Unfortunately, most businesses still use traditional warehousing models and focus on warehousing costs rather than planning.
However, warehouse operations are desired to be more efficient, use less energy, and be more flexible in the future.
It is necessary to focus on more modern, innovative and non-traditional warehouse deployment models than traditional deployment models.
Aisle designs that provide access to products in non-traditional innovative warehouse layouts are different from traditional warehouse aisle designs.
A key motivation for unconventional warehouse design research is to reduce product access distances to reduce in-warehouse cycle time.
Importance of Stock Control and Management Operations
What is Stock Control and How is it Done?
Stock control means regularly monitoring your total product quantity and taking appropriate action by identifying your needs. Stock control covers a process that extends from production to sales. Companies categorize their existing products to identify low and high goods. Inventory control management also determines and plans ahead how much product to keep in order to continue production or sales. Should I order products, continue production, will customer demand increase, etc. such questions apply to warehouse management operations. The stock status of your products is critical to your business’s profitability, campaigns and logistics processes. With inventory control, you can both keep enough inventory to meet customer demand and take steps to reduce storage costs.
The stock report function allows you to track in detail the movements and changes of products and materials in the warehouse. It helps to control the entry and exit, price and movement history of each product;
The stock balance function helps determine the current quantity, cost, and stock sources of products and materials in the warehouse. It helps to accurately track and manage the warehouse products of the enterprise. The stock analysis function also analyzes product movement and product orders. It helps to determine the fundamental product structure and sales trends by analyzing the sales movements, usage and other data of the products.
Warehouse Management Systems: Technological Development and Automation
Automation of warehouse work increases the efficiency of the warehouse storage process to a high level. The benefits of automation are undeniable. First of all, the time spent on goods entry and exit, registration, and inventory is reduced several times. Most importantly, since the human factor is reduced to a minimum after automation, not only the speed of collecting information about goods, but also the correct entry of information is achieved. Automating the registration makes it possible to reduce the personnel working in this area. The work of experts is optimized and can be easily controlled when needed. In addition, automation enables rational use of space.
Automation of warehouse work serves to increase the competitiveness of the company. What does this popular phrase mean today? Under the name of automation of warehouse work, first of all, the application of modern information technologies, which includes many necessary functions, is understood. If the numbers of the cells where the goods are placed are entered into the system, it will be easy to find the goods when they are needed. At the same time, it will make it easy to decide where to place it when it is purchased again, and you can always have the right information about empty cells.
It is possible to classify storage types under three main headings. Storage types vary depending on the exposure of the product to air. There are three types of storage areas: open air warehouses, closed air warehouses and cold storage warehouses. Warehouse operations are complex processes that involve various hazards in terms of occupational safety and health. In terms of labor protection and safety, it is important to inform warehouse managers about the factors that can create risks in warehouse activities and to ensure that necessary measures are taken and implemented in this regard. Occupational health and safety risks in a warehouse can arise from the structure of the warehouse building, handling equipment or the structure of the stored products.
5 points to consider in storage systems and warehouse management
- Maintain optimal stock levels. …
- Reorganize the floor plan of your storage space. …
- Control the movement and storage of assets. …
- Use automation wherever possible. …
- Plan for loops.
Storage processes are generally investigated in five stages. These stages are: (1) the goods receiving process, (2) the goods movement in the warehouse, (3) the picking process, (4) the order picking process, and finally (5) the goods movement process from the warehouse.
Source – SG Logistics